This is where so much time, effort and money is lost. Doing it right the first time, not having rework, call backs, defects and warranty issues, is obviously a huge cost saving!
It takes a range of tools to make this happen. A detailed scope of work connected to your contract is key. The scopes should be trade and builder supervisor friendly, which is easy to read, using diagrams, details, photos to explain the situation. The trades should be an integral part of the team writing the scopes. The scopes should also be have clear objective measures i.e. citing not a vague ‘leave an expansion gap’ but a precise measurement for the gap.
Having checklists (which we have discussed in an earlier blog) that the trades use. The trades should be inspecting THEIR work the builder shouldn’t be doing that; the builder should just be ‘auditing’ the work. Why isn’t the trade doing the job as contracted and expected?
The checklists are important; they are the starting point for data collection so you know at pre-walk for example how many defects you have. If you don’t know that then how do you know if you are reducing defects over time and improving? With data you can focus on your top recurring defects and work closely with the trades to uncover the problem. Often it isn’t one groups fault, it may be a problem with details, communication so be open minded and take a ‘working relationship’ approach not a ‘place the blame’ approach.
Setting the expectations of customers is also critical, this is about the customer understanding the process, the properties of materials i.e. expansion, drying out etc. During the final walk through with the customer is NOT the time to start explaining issues and setting expectations, it’s all over at that point.
A key question with quality is what are you doing for prevention and correction?
Always start with preventing problems FIRST and when they DO occur, correct them and immediately start on prevention again. WHY did it occur, what is the root cause and lets prevent it happening again. This is NOT just with construction but in every aspect of your business!
One way to think about your construction process from a broader view point is SIPOC. Suppliers, Inputs, Process, Outputs and Customers. Have you all of these aspects covered?
NEXT TIME, Trade Relationships.
About the Author
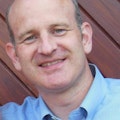
Denis Leonard
Denis Leonard has a degree in construction engineering an M.B.A. and a Ph.D. in quality management. Denis is a Fellow of the American Society for Quality, a Certified Quality Manager, Auditor and Six Sigma Black Belt. He has been an Examiner for the Baldrige National Quality Award Board of Examiners a Judge on the International Team Excellence Competition and a Lead Judge on the National Housing Quality Award. A former Professor of Quality at the University of Wisconsin, he has experience as a quality manager in the homebuilding industry as well as construction engineer, site manager and in training, auditing and consulting with expertise in strategic and operational quality improvement initiatives. His work has achieved national quality, environmental and safety management awards for clients.
Denis is co-author of 'The Executive Guide to Understanding and Implementing the Baldrige Criteria: Improve Revenue and Create Organizational Excellence'.
http://www.BusinessExcellenceConsulting.net
Full listing of blogs https://www.probuilder.com/author/denis-leonard