For over 10,000 years, timber has been used as a primary source for construction materials, a trusted leader among building products with an incumbency spanning from the Neolithic age to the 21st century. Even in an era of fast innovation and cutting-edge product development, 91% of all U.S. homes were framed with wood in 2020, according to NAHB. Rather than swaying from the reliable durability of timber in new home construction, some building product manufacturers and builders themselves are instead using heat to modify wood for improved performance, increased flexibility, and lasting sustainability. How’s that for a hot commodity?
As a natural hygroscopic material—able to absorb or repel water until it reaches an equilibrium—timber expands and contracts when subjected to different heat settings, but manufacturers can use that science to their advantage in order to manipulate the form and appearance of wood as a building material.
Thermal Modification
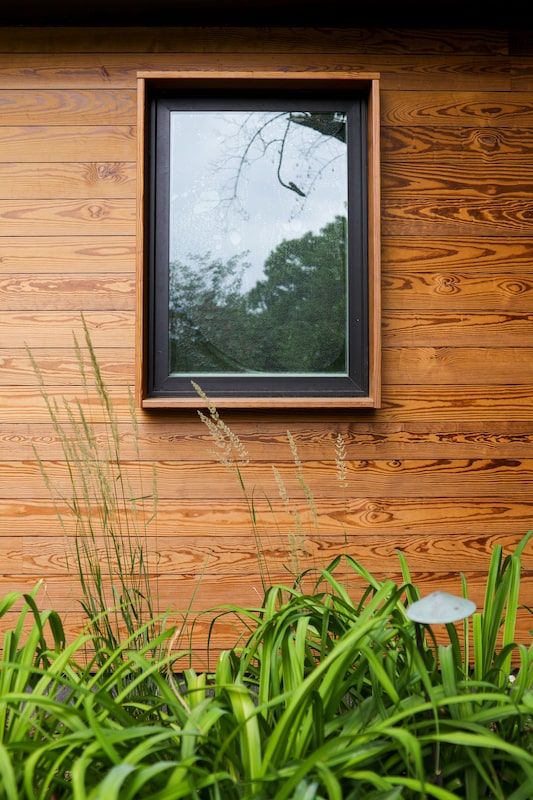
Thermal modification is the process of heating wood at temperatures between 160 and 240 °C to alter the cell wall moisture content, and thus, the overall durability of the product. According to the Journal of Materials Science, thermal modification results in a material that is “darker in color, has improved dimensional stability, and microbial resistance compared to unmodified wood,” but where do those properties come into play during the heating process?
Hardwood and softwood lumber can be heated either to retain moisture through steam modification or to lose absorbed water in treatment atmospheres using nitrogen or ambient air. Intermittent heating stages throughout the thermal modification process shock the wood and all of its cell wall polymers, essentially locking the wood into a rigid, inflexible form, the Journal of Materials Science says.
Not only is the strength of wood improved through the heating process, but all food sources (sugars) for mold and bacteria are also removed from the wood, making thermally modified wood (TMW) a safer alternative to traditional lumber products. Duluth, Minnesota-based Arbor Wood Co. is taking its TMW products one step further by eliminating resin and chemical agents from the final stages of development to create a fully biodegradable material at the end of its lifespan.
Heat Bending
For centuries, lumber has been a top choice for framing due to its unbending nature, but when exposed to high heat and steam, hardwoods and softwoods can be shaped and molded into just about any form.
The straw-like cell walls that made up wood’s biology are comprised of 50% cellulose and 30% lignin. When wood is heated to a high temperature, clumps of cellulose molecules slide past each other, allowing wood to bend with an otherwise unnatural flexibility. After the wood cools off, lignin molecules bond to the cellulose in the new reinforced structure, allowing the sculpted wood to hold its shape unless reheated.
Because all wood has mostly the same biology, any species of hardwood or softwood can be steam-bent to some extent. Whether crafting furniture or creating artistic accents for the home, steam bending is an efficient way to mold lumber without sawing, gluing, or cleaning up. All it takes is some mind-bending creativity and a whole lotta heat.
Hot and Cold Open Tank Treatment
Lumber is one of the most durable building materials used around the world for residential and commercial construction projects, but just like any other natural resource, it’s also susceptible to rot and decay over time. In order to treat and preserve wood used for construction, hardwood and softwood products can be soaked and steeped in hot and cold water tanks to absorb added preservatives.
The open tank treatment consists of immersing wood “alternately in separate tanks containing heated and cold preservative, either oil- or waterborne (or in one tank which is first heated then allowed to cool),” according to the Kentucky Pesticide Safety Education Program. The hot bath forces the wood to expand, opening a pathway for preservatives to penetrate through the outer surface and into a network of inner fibers. In the cold bath, the air inside of each log or plank contracts to create a vacuum that seals the treatment inside for lasting durability.
Thermal treatment processes vary depending on the types of wood being soaked, but all have been proven to prolong the lifespan of engineered wood and keep out parasites when tested against the elements over an extended period of time.
Shou-Sugi-Ban (Wood Charring) 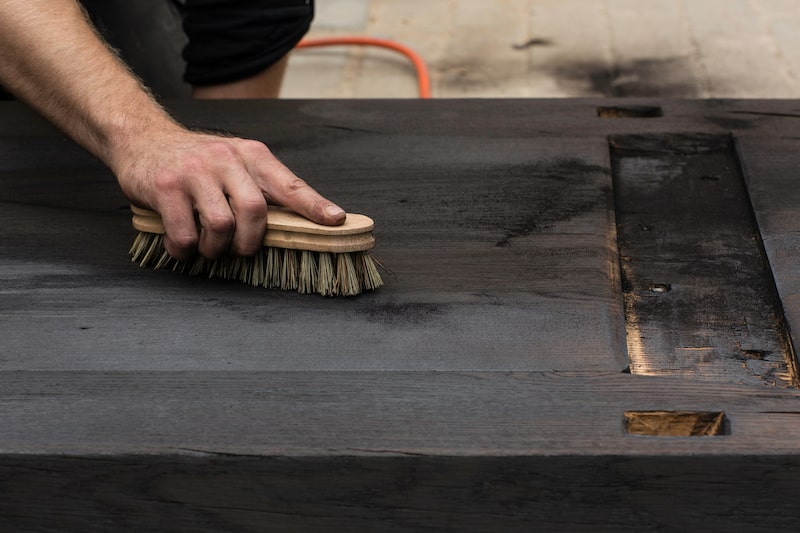
The concept of shou-sugi-ban originated in Japan in the 18th century as a method for weatherproofing cedar siding, and the practice is still very much alive in the 21st century, though its purpose has evolved and changed over the past several centuries. Shou-sugi-ban involves charring light, porous wood such as cedar to create a low-maintenance, waterproof product used widely for siding or for outdoor furniture.
The process of wood charring starts with a high-intensity flame from a torch, which is blasted onto the surface of the wood for roughly ten seconds (or until a layer of black soot forms). The charcoal is then dusted off with a wire brush and the final product is cleaned and sealed with oil for a smooth and impenetrable finish.
When properly maintained, the life expectancy of shou-sugi-ban is estimated at over 80 years, but when used externally for cladding, it should be oiled every 15-20 years.
Kiln Drying
Every type of wood is prone to warping, cupping, and splitting depending on changes in humidity, but to bypass those adverse reactions and properly prep lumber for machining, gluing and finishing, builders should first dry softwood and hardwood lumber using a kiln. The kiln drying process controls temperature and air circulation to reduce moisture in lumber products, converting water content into vapor.
Dehumidification kilns are most commonly used in the lumber industry due to their efficient recycling of heat, making them more cost-effective compared to traditional kilns, which filter out hot air and water vapors. Dehumidification kilns circulate hot air over wood at a temperature between 95 and 100 °F, at which point moisture is secreted from the timber before evaporating and being condensed into liquid form on refrigeration coils.
Kiln dried wood is much longer lasting than untreated lumber products, making it a first step for many builders looking to construct durable homes or other load-bearing structures. Furniture makers also favor kiln dried timber for its lengthy lifespan and its ability to retain resins and stains.
Related Stories
Custom Builder
Improve Thermal Performance and Lower Costs
An optimized, value-engineered approach to framing kills two birds with one stone
Education
DuPont Debuts Podcast About Residential Building Trends Featuring Industry Leaders
Building Materials
Benjamin Obdyke Liquid Flashing
Benjamin Obdyke has expanded its line of flashing with the addition of a liquid-applied product
Framing & Building Envelope
Moisture Protection Screen
Provides added protection against moisture and mold and allows for increased ventilation and drainage